Breaker pressure relief, also known as leakage, is one of the frequent failures. Once the breaker breaks pressure, the system pressure cannot be established, and it will cause environmental pollution, increase downtime, reduce productivity, increase production costs, and affect production. , And even produce immeasurable serious consequences. So what caused the leak of the breaker?
1. Selection of seals. The reliability of the hydraulic breaker depends to a large extent on the design of the seal and the choice of the seal. Due to the unreasonable selection of the sealing structure and seals in the design, the design did not consider the compatibility of hydraulic oil and sealing material, load conditions, pressure, working speed and environmental temperature changes, which will directly or indirectly cause hydraulic pressure to varying degrees. Leakage of the system. In addition, due to the presence of dust and impurities in the operating environment of the hydraulic breaker, suitable dust seals should be selected in the design to prevent dust and other dirt from entering the system, contaminating the oil and damaging the seals, resulting in leakage.
2:In the design, the geometric accuracy and roughness of the moving surface are not carefully enough, and the strength of the connector is not checked in the design, which will lead to leakage in the work of the crushing hammer
3:The barbaric assembly operations should be stopped. If the parts are deformed due to excessive force, they should be carefully checked before assembly. A small amount of hydraulic oil should be immersed in the assembly process and gently pressed in. Diesel oil should be used for cleaning, especially rubber parts such as seals, dust rings and O-ring. If it is cleaned with gasoline, it is easy to age, lose its original elasticity, and reduce the sealing function.
4:All hydraulic components and seals of the breaker have strict requirements on dimensional tolerances, surface treatment, surface roughness, shape and position tolerances. If the manufacturing process exceeds the tolerance range, such as the diameter of the cylinder and piston, the depth or width of the seal groove, the size of the hole where the seal ring is installed is out of the tolerance range, burrs or depressions, and the chromium plating layer falls off. The seal will be deformed, scratched, squeezed or improperly squeezed, so that it will lose its sealing function, and the parts will have congenital leakage points, which will cause leakage after assembly or use.
5:During the working process of the breaker, the drill rod is exposed. Although the dust ring and seal are installed in the front center hole of the middle cylinder, dust will inevitably be brought into the breaker, which will accelerate the abrasion and wear of the seal and piston, which will lead to leakage.
6:At atmospheric pressure, air can be dissolved in the hydraulic oil, but under the high pressure of the hydraulic system, more air or other gases will be dissolved in the oil. Air forms bubbles in the oil. After the piston hits, the pressure in the back cavity changes rapidly between high pressure and low pressure in a short period of time, which will cause the bubbles to generate high temperatures on the high pressure side and burst on the low pressure side, and the hydraulic oil rushes to the surface of the piston at high speed. Accelerate surface wear and cause leakage.
7:Due to the humid working environment and other factors, water may enter the hydraulic breaker and react with the hydraulic oil to form acidic substances and sludge, thereby reducing the lubricating performance of the hydraulic oil, accelerating the wear of parts and causing leakage.
8:The seal is made of oil-resistant rubber and other materials, which will cause system leakage after aging, and cracks and damage will occur after long-term use. If the parts are damaged by collisions during work, the seals will be scratched, resulting in leakage.
9:Only by doing the daily inspection and maintenance work of the breaker can we try our best to reduce the occurrence of leakage, without affecting the efficiency of the entire production, and doing every small step to ensure the normal use of the entire large equipment.
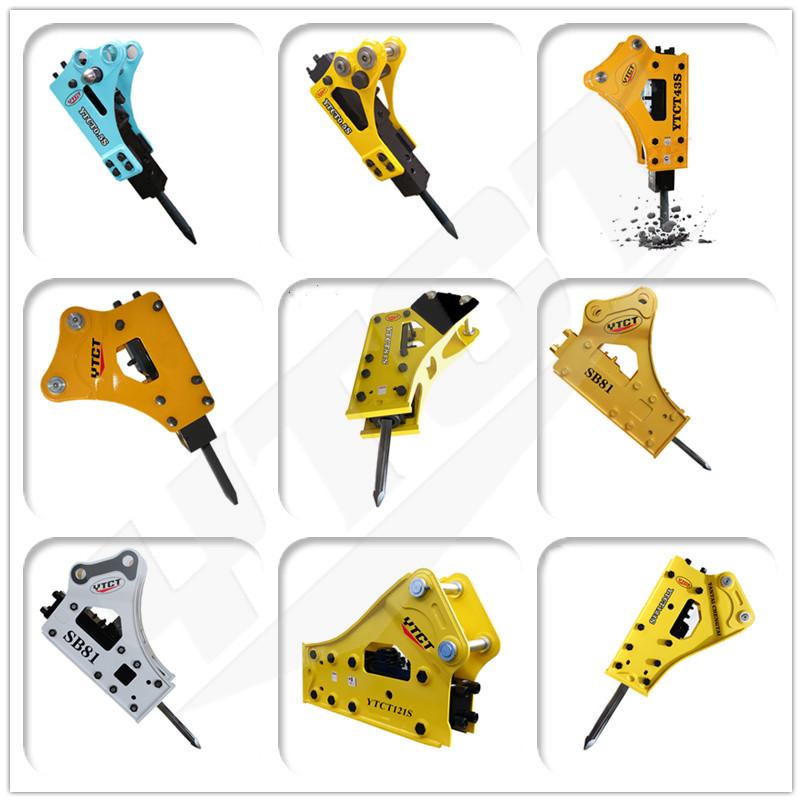